Over 100 days of campaign
It’s all about the sugar content
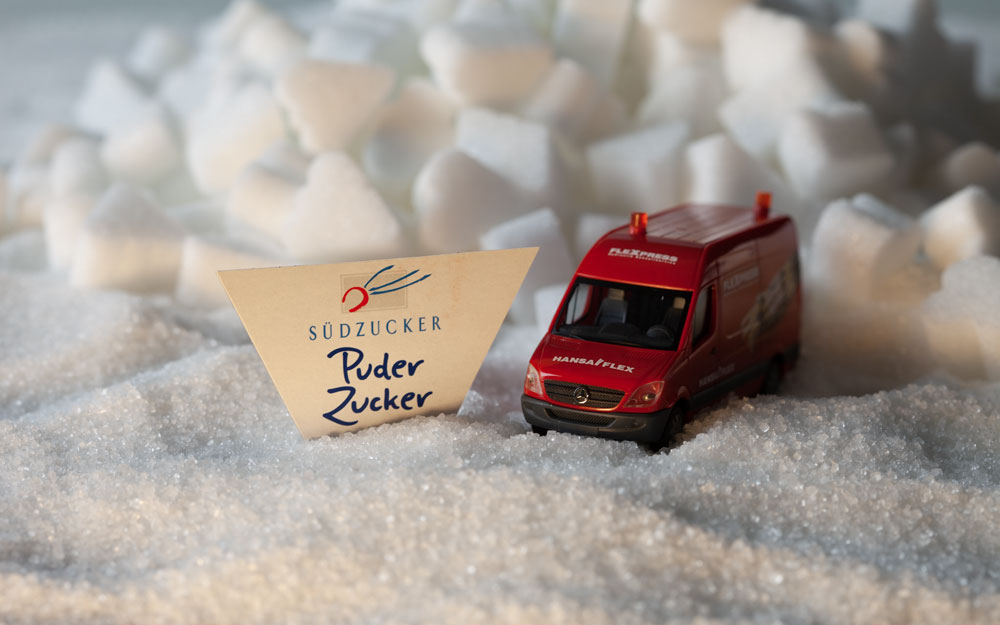
From the beet to the coffee cup
Crystallisation
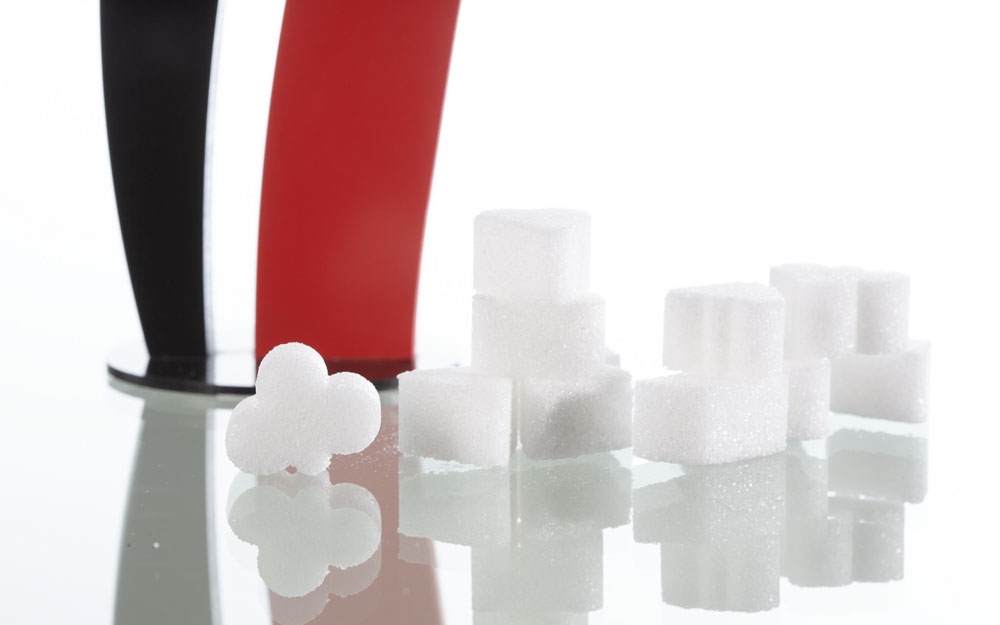
Further processing and sustainability
From the seal to the metal hose
Sugar in record time
With figures like these, it is clear how disastrous a machine failure would be during the campaign. So non-campaign time is used for extremely thorough maintenance. And if a machine does develop a fault during the campaign, the workshop managers at Südzucker know that HANSA‑FLEX's mobile Rapid Hydraulic Service will be there in double-quick time.