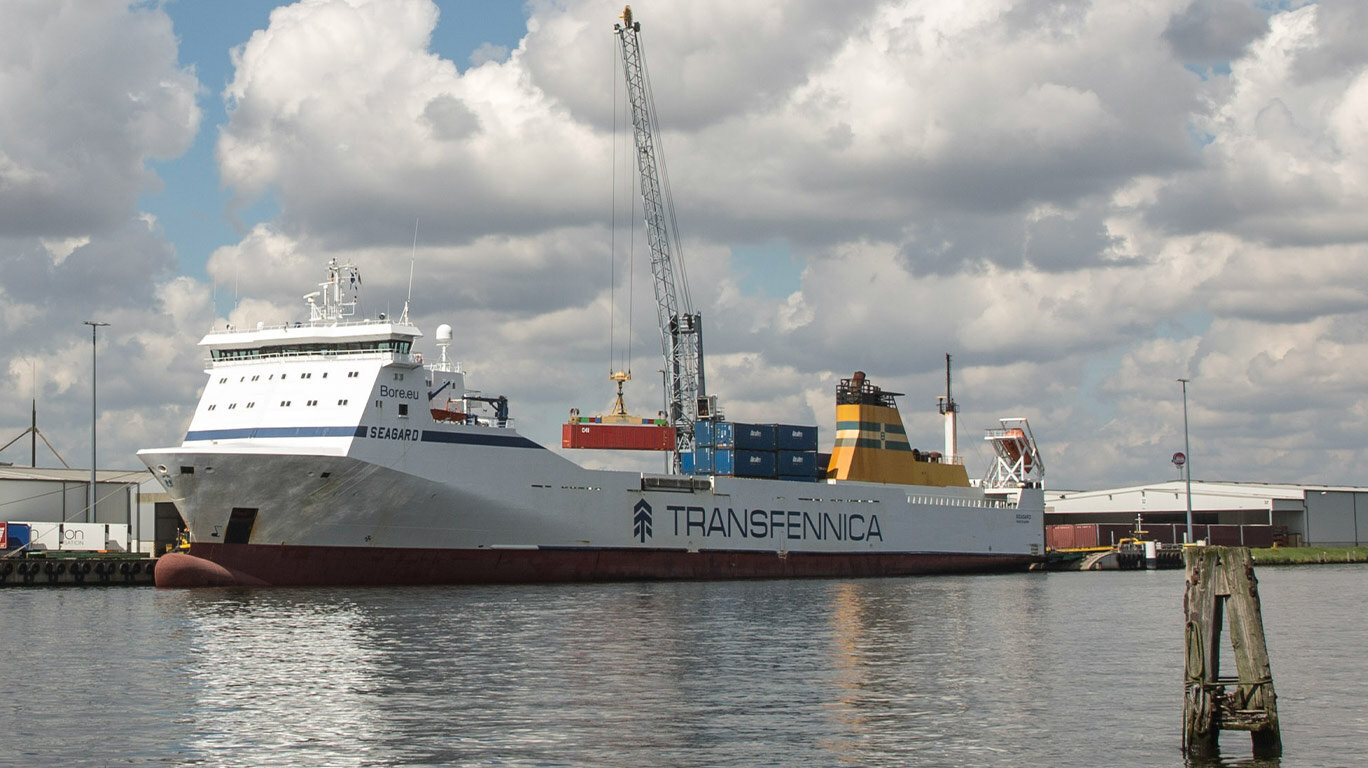
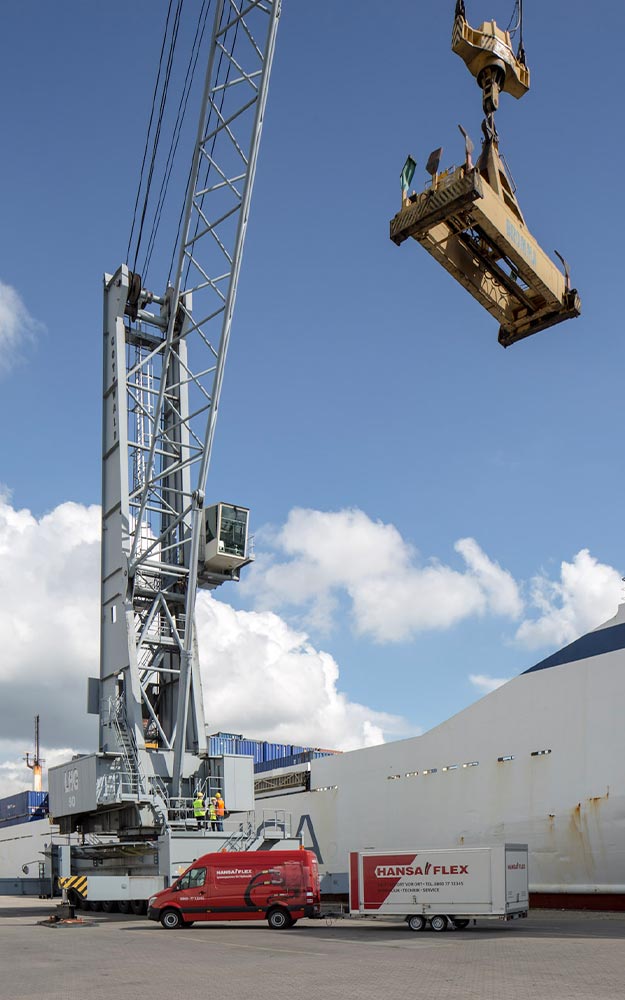
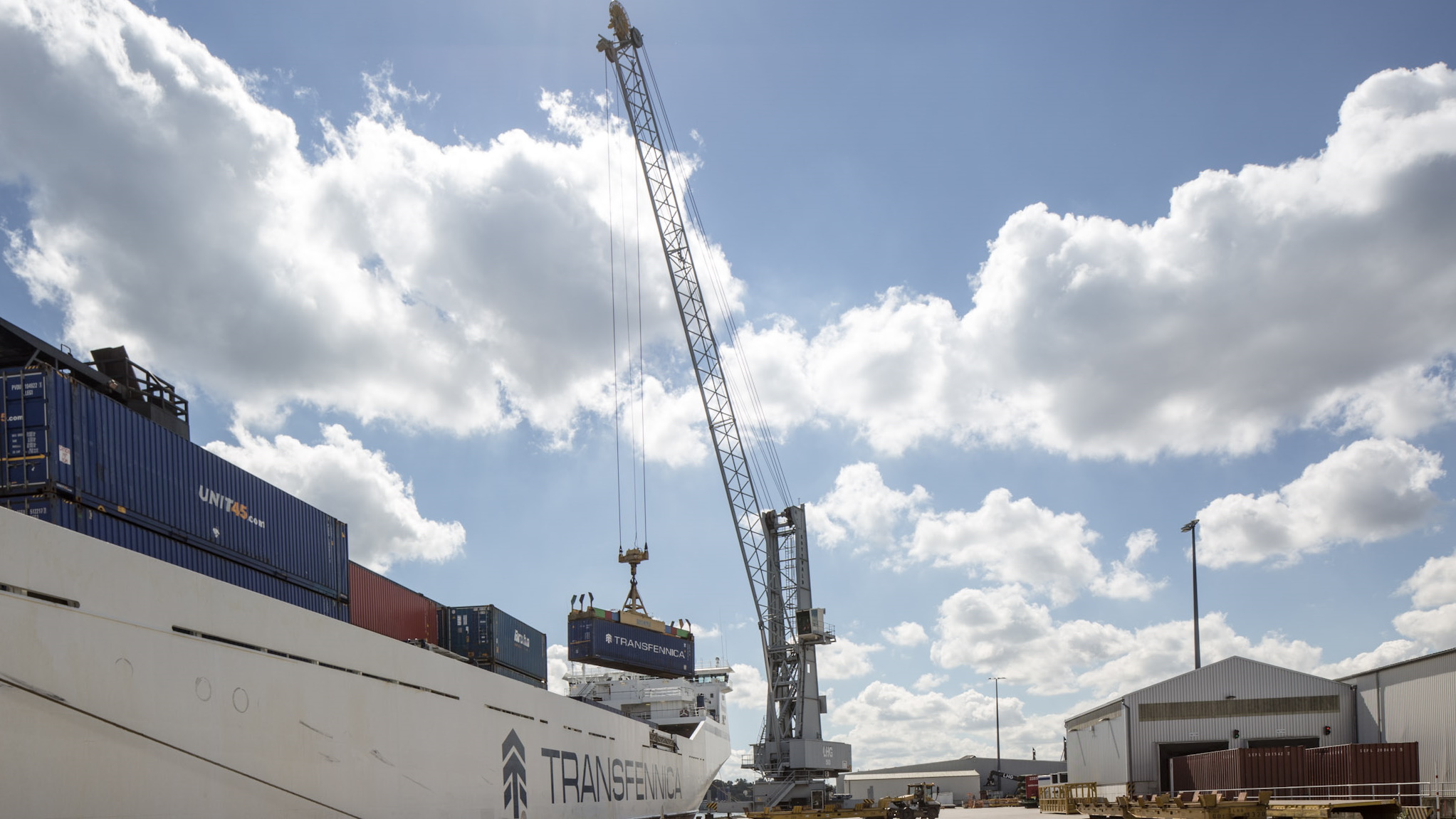
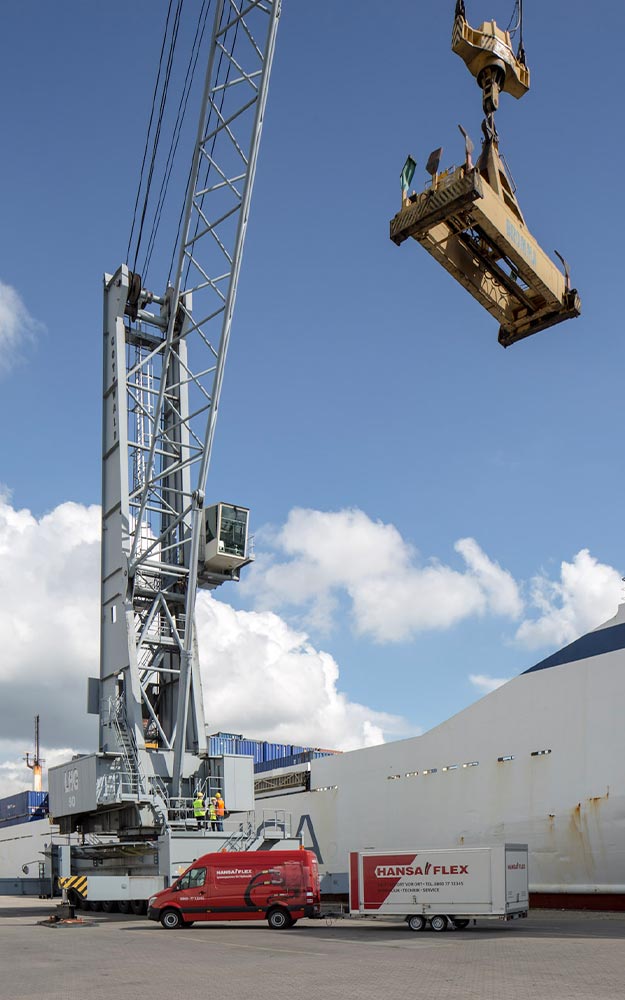
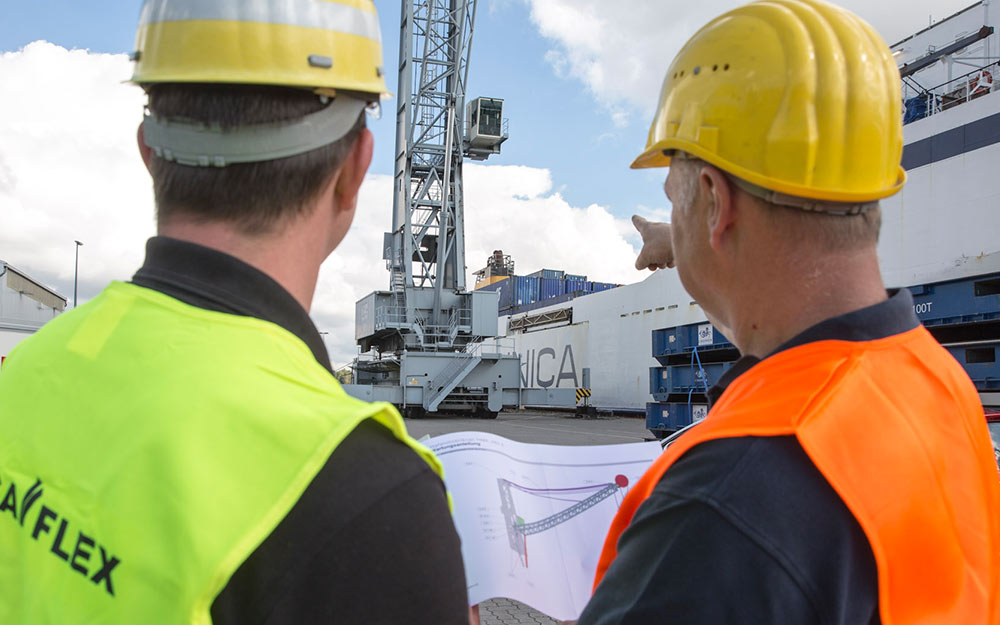
Precision solutions
Heavy loads
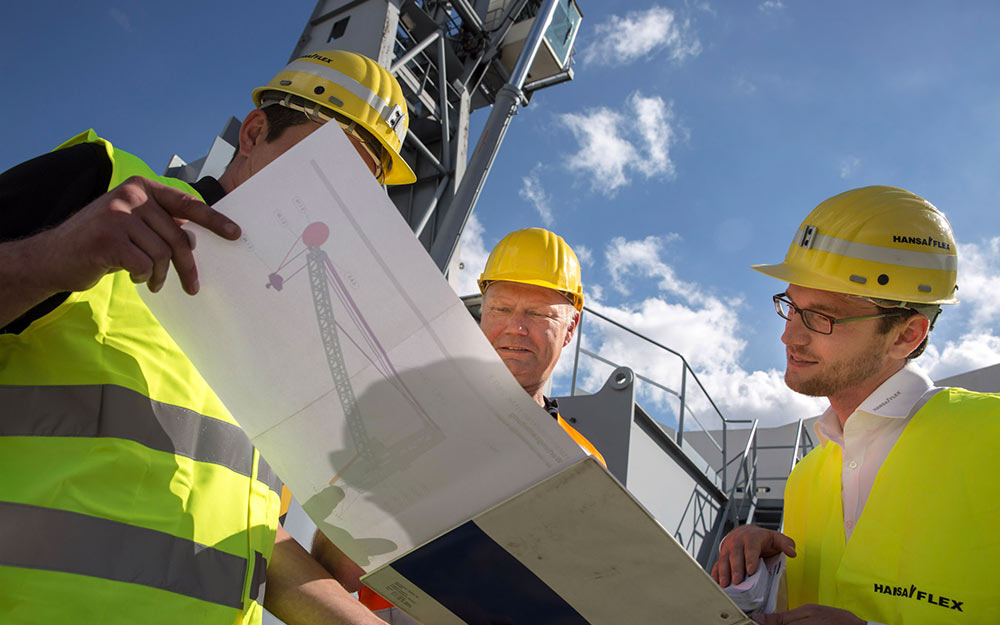
Do you have any questions about our services and products? Or do you need help?
Sundays and public holidays are excluded
HANSA-FLEX repairs the cylinder on a 100-tonne crane for Lübecker Hafen-Gesellschaft
With around 75 million passengers a year Heathrow is the largest airport in Europe. Highly specialised ground handling companies ensure that everything runs smoothly. Taking care of the hydraulics is the job of the HANSA-FLEX Heathrow branch.
At the gates to Lübeck’s old town, an enormous crane loads containers onto ships destined for St. Petersburg and Northern Finland. When the giant’s main cylinder threatened to fail, HANSA-FLEX took charge of the repair.
Just a stone’s throw away from Hamburg airport is a city within the city – the head office of Lufthansa Technik AG. HANSA-FLEX supplies a large number of products, including several that are incorporated into the test benches.